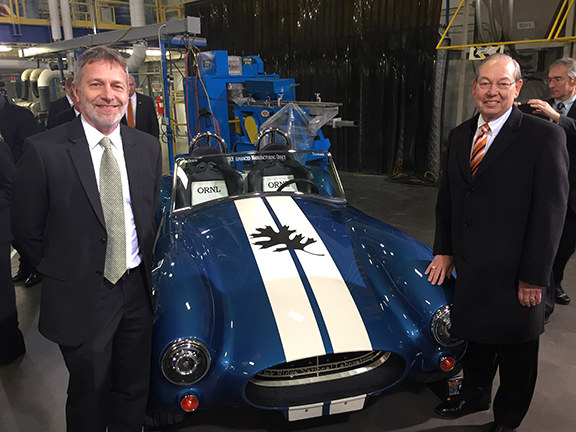
University of Tennessee Knoxville Chancellor Jimmy G. Cheek, right, stands with Martin Keller, associate laboratory director at Oak Ridge National Laboratory, in front of a Shelby Cobra printed as a collaboration between ORNL and UT personnel. The car served as a highlight of President Obama’s visit to the area on Friday. (Photo courtesy UT)Â
KNOXVILLE—President Obama’s announcement on Friday that the University of Tennessee in Knoxville would be the lead institution in a $259 million advanced composites manufacturing project known as the Institute for Advanced Composites Manufacturing Innovation, or IACMI, was met with applause, but also a few questions.
Many wondered what advanced composites manufacturing really means, why the UT-led consortium was selected, and what the impact for the area might be.
Here are some answers.
What is IACMI?
IACMI is the newest federally funded institute for manufacturing innovation. Its focus is on advancing innovation in the manufacturing of composites used in automobiles, wind turbines, and compressed gas storage tanks.
Related video:Â https://www.youtube.com/watch?v=VobUkNKpCGE
IACMI has three composites application centers directed to specific industrial applications. These centers are located in Michigan (automotive), Colorado (wind), and Ohio (compressed gas storage), with enabling technology centers in Indiana (modeling and simulation) and Tennessee (composite materials and process technology).
These states, along with Kentucky, are the six core partner states of IACMI, which also involves a 122-member consortium that includes industry leaders, universities, and national laboratories such as fellow founding partner Oak Ridge National Laboratory.
In addition to $189 million in funding from those partners, $70 million came from the U.S. Department of Energy’s Advanced Manufacturing Office within the Office of Energy Efficiency and Renewable Energy.
The funds will be used to establish this newest institute for manufacturing innovation. UT’s Vice Chancellor for Research and Engagement, Taylor Eighmy, serves as the principal investigator, while ORNL’s Craig Blue is the chief executive officer of the institute.
The day-to-day operations of the institute will be managed by a new not-for-profit 501(c)(3) organization established by the UT Research Foundation and located in Knoxville.
The institute staff will coordinate activities across the six states and five centers, interact with the other national institutes, focus on research and development project selection with corporate partners and researchers, manage workforce development and education efforts, and ensure the Department of Energy’s goals in advanced composites manufacturing are met.
On the industry side, members include Volkswagen, Ford Motor Company, Dow Chemical, DowAksa, Boeing, Lockheed Martin, Dassault Systemes Americas Corp, the Strongwell Corporation, and Local Motors, among others.
“This project will accelerate the development of an advanced manufacturing system in East Tennessee, particularly around automotive manufacturing and materials development,” Eighmy said. “Increasingly, we are seeing keen interest in the development of low-cost carbon fiber for use in composites, their use in new composite materials and manufacturing technologies, and how these become integrated in hybrid material—containing both composites and metals—in manufactured products.”
What is advanced composites manufacturing?
Advanced composites manufacturing typically involves the use of revolutionary materials, such as carbon and glass fibers, or processes, such as the 3D printing technique used to print the Shelby Cobra on display during Obama’s visit.
Composites are made by combining a polymer resin with strong reinforcing fibers, typically glass or carbon. This process results in a composite material with enhanced overall performance, including improved strength and stiffness.
Historical demand for composites has been for low-volume, high-value industries such as aerospace. High-speed production at lower cost could enable broader use of composites in high-volume, cost-sensitive markets such as automotive, wind energy, and compressed gas storage.
For example, making lighter weight vehicles is an important energy efficiency strategy in transportation. A 10 percent reduction in vehicle weight can improve fuel efficiency by six to eight percent for vehicles with conventional internal combustion engines.
“Being the lead institution on this project is a testament to the ideas, research and faculty that we bring to the table,” said Wayne Davis, dean of UT’s College of Engineering.
“From our expertise in developing the materials of the future to our work in advanced manufacturing techniques and 3D printing, our college has a wealth of expertise that we can share with the institute, and that really shows in our selection to lead that enterprise.”
Why was UT picked to lead the project?
UT has many core partners that it is working with on this project: ORNL, the National Renewable Energy Laboratory, Michigan State University, the University of Dayton Research Institute, Purdue University, and the University of Kentucky.
UT has emerged as a growing force in the field, as evidenced by the ongoing partnership between UT and ORNL, its long history in nonwoven composites, its extensive collaboration with the federal government on composites research and development, and the selection of Suresh Babu as UT-ORNL Governor’s Chair in Advanced Manufacturing.
Several departments within the College of Engineering in particular have focused on advancing the use of materials in manufacturing and the process itself.
Carbon fiber, additive manufacturing (3D printing), and the development of other materials are but a few of the areas where UT and ORNL have a shared wealth of knowledge.
“Having IACMI will not only help cement expertise in traditional manufacturing, but will bring together UT’s expertise in design, polymer science, textiles, processing of composites, as well as testing and characterization of composites,” said Babu, who works out of UT’s Department of Mechanical, Aerospace, and Biomedical Engineering as well as ORNL.
“This unique partnership will advance the deployment of polymer composites to provide benefit to member companies, as well as train the future high tech workforce.”
What might the impact be?
In terms of economic impact, IACMI’s analysis has shown that the market for composite materials will nearly double globally by 2020.
Making sure that workers, employers and suppliers in the U.S. are able to stay ahead of the curve on the process is seen as crucial by industrial, academic, and political leaders across the spectrum.
Additionally, the “green effect” of decreasing both the amount of materials needed to produce a product and the energy to run it should save consumers and producers alike.
Socially, the promise of composites as stronger, lighter materials could impact everything from cars to medical devices, with an increase in durability extending the life of both.
One of the key objectives of the plan is supporting American manufacturing and raising the profile of industries in the U.S. as production processes change, which is both a highlight of Obama’s upcoming State of the Union address as well as a reason for his visit to East Tennessee.
For more on IACMI, visit http://iacmi.org.
Leave a Reply